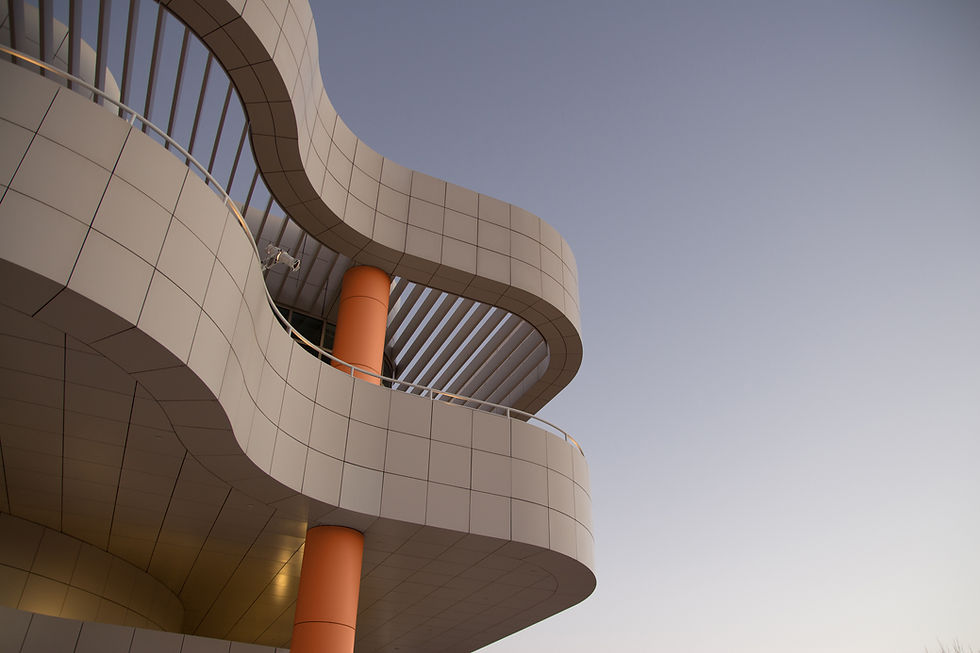
Case Study: Enhancing Team Performance and Goal Alignment for a Premier German Automotive Manufacturer
Oct 29, 2024
2 min read
1
9
1

Client: One of Germany’s premier automotive manufacturers
Duration: 5 Years
Background:
The client, a leading automotive manufacturer in Germany, faced increasing demands to meet production and business goals in a competitive global market. To achieve these objectives, the organization required both technical training for its production team and development in team alignment to ensure that its strategic goals were consistently met.
Objective:
To train and develop the manufacturer’s team in both technical and organizational aspects, ensuring that they could meet production demands while aligning with the company’s broader business goals and meeting critical timelines.
Challenges:
Technical Skill Gaps: The organization needed to ensure that its team had the necessary technical expertise to maintain the highest standards in automotive production.
Team Alignment: There were challenges in ensuring that various departments within the organization were aligned with the company’s overall strategic objectives.
Meeting Timelines: The manufacturer needed to meet strict production timelines to stay competitive in the fast-moving automotive industry.
Solution Approach:
1. Technical Training Development
I worked closely with the production team to enhance their technical skills, focusing on:
Hands-on technical training to improve the team's proficiency in advanced automotive production technologies.
Tailored training programs to address specific technical challenges unique to the manufacturer’s production processes.
Continuous feedback and assessments to ensure skill retention and improvement over time.
2. Team Development and Goal Alignment
To address the need for team alignment with business goals, I implemented development programs that focused on:
Workshops to help team members understand and align with the company’s broader business objectives.
Leadership training for key team members to foster better communication and decision-making across departments.
Facilitating cross-functional collaboration to ensure that all teams worked cohesively toward common business goals.
3. Timeline Management and Efficiency Improvement
I worked with the team to develop systems and processes that ensured:
Timelines were met by improving workflow efficiencies and minimizing production bottlenecks.
Regular performance reviews and process adjustments based on real-time data to keep the team on track.
Strategic planning sessions to align short-term actions with long-term business goals.
Results:
1. Enhanced Technical Capabilities
The team gained the technical expertise required to meet the manufacturer’s high production standards, resulting in improved product quality and operational efficiency.
2. Stronger Team Alignment with Business Goals
The workshops and leadership training resulted in better team cohesion and a stronger understanding of the company’s business objectives. Cross-functional collaboration was greatly enhanced, improving decision-making and execution.
3. Improved Timeline Adherence and Efficiency
By optimizing workflows and enhancing team development, the organization was able to consistently meet its production timelines, boosting its ability to meet market demand and maintain its competitive edge.
Conclusion:
Over the course of five years, I successfully trained and developed the team at one of Germany's premier automotive manufacturers, focusing on both technical skills and team alignment. These efforts helped the organization meet its business goals, improve operational efficiency, and consistently deliver on time, positioning them for long-term success in a competitive market.
What a transformative journey! 🚀 Balancing technical excellence with strategic alignment is no small feat, and it sounds like this structured approach yielded remarkable results in both quality and team cohesion. Your emphasis on aligning technical training with broader business goals highlights a key neuroleadership principle: connecting individual actions with organizational purpose can drive both motivation and engagement. 💡
In your experience, which aspect—technical skills or team alignment—has the most immediate impact on operational efficiency?