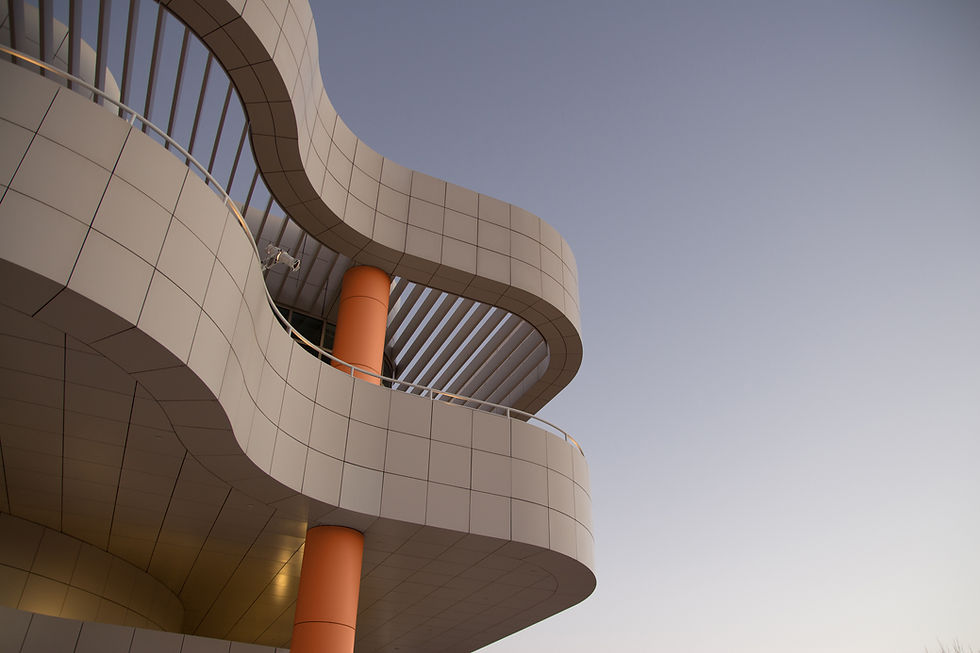

Background
A leading global materials science company, renowned for its innovations in glass, ceramics, and related technologies, faced the challenge of introducing a new product to market while optimizing its manufacturing processes. With operations spanning multiple continents, the company needed to align its global teams, improve production workflows, and ensure timely product launch while maintaining the highest industry standards.
Objective
The primary objective of the collaboration was twofold:
Optimize manufacturing processes to increase production efficiency and reduce time-to-market for the new product.
Enhance team collaboration and performance across global sites, ensuring that all stakeholders were aligned with the company’s business goals and operational strategies.
Approach
To achieve these objectives, I worked closely with the company over several years, leveraging a combination of strategic technical training and operational development initiatives.
Technical Training:
I developed and led customized technical training programs focused on improving manufacturing workflows, quality control, and product development processes.
The training was delivered to diverse teams across various global locations, ensuring that all personnel understood the latest technologies and best practices in the field.
Special emphasis was placed on cross-functional training, enabling teams to develop a broader understanding of different aspects of production, which fostered better collaboration.
Operational Development:
I collaborated with senior management to streamline production workflows by identifying bottlenecks and implementing more efficient processes. This included refining supply chain management, automating specific tasks, and optimizing resource allocation.
The operational development plan also included setting measurable performance metrics to track progress toward meeting the company’s key business objectives.
Communication channels between teams across locations were enhanced, ensuring a unified approach to problem-solving and decision-making.
Aligning Global Teams with Business Goals:
A key aspect of this collaboration involved aligning global teams with the company’s overarching business strategy. This was done through workshops, strategy sessions, and ongoing engagement with key stakeholders.
I worked closely with the leadership teams at each location to ensure that the company’s vision, mission, and objectives were clearly communicated and understood at all levels.
Ensuring On-Time Product Launch:
With optimized workflows and aligned teams, the company was able to meet critical milestones, ensuring the new product’s timely market release.
Quality assurance measures were put in place to maintain the high standards the company was known for, ensuring that the product met both internal and external requirements.
Results
The collaboration produced significant improvements across multiple areas:
Increased Production Efficiency: By streamlining manufacturing processes and implementing best practices, the company saw a marked improvement in production efficiency. This allowed them to reduce the time-to-market for the new product while minimizing operational costs.
Enhanced Team Collaboration: Through training and better communication, global teams became more cohesive and collaborative. This improved cross-functional problem-solving and led to more efficient decision-making.
Successful On-Time Product Launch: Despite the complexity of the product and the coordination required across multiple sites, the company successfully launched the new product on time, meeting customer and market demands.
Positioned for Continued Growth and Innovation: With improved workflows, stronger teams, and a successful product launch, the company was better positioned to continue its growth and maintain its status as an industry leader in materials science.
Conclusion
This long-term partnership not only enabled the company to meet its immediate goals of product launch and process improvement, but it also laid the foundation for future innovations. Through strategic technical training, operational development, and team alignment, the company was able to optimize its performance and stay competitive in a rapidly evolving industry.